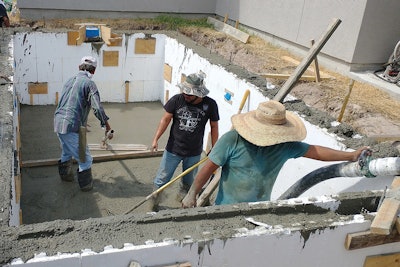
It might be counterintuitive, but there are actually a growing number of systems available to build concrete pools. Many of these systems have evolved from civil concrete construction — buildings and bridges and the like.
While plaster/gunite and traditional poured concrete dominate the market today, there are new materials and new ideas going into the ground all the time, and some of them have attractive features like low cost and faster install times. Here's a couple you may not have even heard of — shuttered reinforced concrete and ICFs.
SHUTTERED REINFORCED CONCRETE
With this method, you pour the concrete into lightweight steel forms, and just leave the forms where they are, providing extra strength to the shell. Shuttered reinforced concrete is a technique used in civil engineering to build bridges, dams, buildings, etc., and after first being introduced for pool building in Europe, this pool construction method has come to the United States.
Mazarena, a company founded by retired civil engineer Jerome Licata, is the exclusive supplier of this system here in the United States, imported from Marinal, a French manufacturer.
Licata himself has a deep personal and professional interest in concrete, having worked in the world of industrial concrete construction for many years. He was researching pool building systems for his own backyard pool project when he came upon shuttered concrete, and was impressed with its capabilities. "I was surprised when I contacted the manufacturer in Europe to discover that the system wasn't available in the States, so I decided I should be the one to start bringing the system to U.S. builders." Licata believes the timing is right for a new system that emphasizes speed and efficiency in the build, along with a structurally solid shell.
FORMS
Shuttered, reinforced concrete was originally created for building earthquake-resistant, multi-level residential houses because the formwork itself provides reinforcement in a shell that is completely interconnected.
The system is composed of two galvanized steel panels — one made of expanded metal with ribs produced from cold-rolled and hot galvanized steel in accordance with ASTM C 847 that forms a mesh on one side — and the second composed of compressed fiber cement board with a cross-sectional area that is installed vertically.
Once the form works are put together in the hole, the concrete is poured between the two panels. The pouring process can be checked visually from top to bottom because the crew can see through the interior steel mesh panel. The formwork remains integrated and acts as reinforcement, thus requiring fewer pieces of reinforcing rebar. The concrete of the walls and of the bottom slab is poured simultaneously, allowing the concrete to set evenly, creating a one-piece joint-less structure.
A ONE-PIECE CONCRETE POOL
Any size and shape pool can be built in this way — rectangles, free-form shapes, contemporary designs, lap pools, infinity pools, and even aboveground or semi-inground pools.
The forms come folded and are very compact. For example, forms for a 20-by-30-foot pool will fit on the back of a pickup truck or a flatbed trailer sitting on one to two pallets. Builders open the forms on the jobsite and set up a railing system around the perimeter of the pool. The panels are screwed into the railing system to ensure they are flush and level.
When pouring begins, crews fill in the forms about halfway up the wall and then vibrate the concrete. During this process, the concrete will 'seep out' at the bottom of the wall/formwork, creating a 'wet-wet' connection between the wall and the (concurrently poured) slab floor.
The pool interior can be finished with a variety of materials, but Licata says that reinforced PVC membrane is most often used in Europe and is the waterproofing interior solution that he recommends. The PVC membrane is welded onsite as soon as the one-piece concrete form is complete.
The company believes the system can appeal to pool builders who are looking for less labor intensive options that will allow them to have tighter control of their construction schedule. Mazarena showed the product both in Atlantic City and Las Vegas.
Stages of an ICF pool build by Aqua Max Plus, Gatineau, Quebec.Photos courtesy DC Pools
INSULATED CONCRETE FORMS (ICFS)
Insulated Concrete Forms (ICFs) are hollow blocks composed of expanded polystyrene foam and plastic bridges, or webbing, which serve the purpose of connecting the block sides. ICF systems have a long history of application in residential construction, particularly in the context of home foundations. This building technique relies on interlocking expanded polystyrene (EPS) foam blocks to establish a framework for reinforced concrete walls. When building a pool wall, ICFs are simply stacked atop each other and fortified with steel rebar, then concrete is poured into the forms. When it hardens, it generates a robust and enduring pool structure. After the concrete cures, the forms stay in place and help insulate the pool, a major plus for builders such as Max Lavio, owner of Aqua Max Plus in Gatineau, Quebec.
"When we started using ICF systems to build our pools, we were immediately attracted to the insulation properties of the product, as it keeps the pool water warmer longer for our clients, which is especially beneficial here in northern Quebec," he says. "The ICF system is more energy-efficient, which can save customers money on their energy bills."
The formwork includes internal webs that provide a continuous insulation layer to eliminate thermal bridging and air leaks. The foam blocks come in various sizes and shapes and can be easily cut to create virtually any pool design.
"They are very versatile and allow us to customize each pool to the backyard, regardless of the property's size or shape," Lavio adds.
DC Pools in Corpus Christi builds an ICF pool lined with a PVC membrane.Photos courtesy Aqua Max Plus
ICF CONSTRUCTION BENEFITS
ICFs gained popularity during the supply disruptions of the pandemic, as ICFs were (and remain) a building material easily sourced. That availability attracted Mark Teinert of DC Pools in Corpus Christi, Texas, another ICF builder who has been working with the method and material. "We initially turned to insulated concrete forms with a PVC membrane interior because the construction materials (foam forms and PVC membrane) are stocked and readily available, enabling us to construct pools quickly and easily for any size yard with resort-style features that are in high demand," he says.
Companies like Aqua Max Plus and DC Pools were also looking for construction solutions with benefits they could easily sell to consumers looking to save money on pool heat, with energy savings estimates of up to 60%. Since the ICF system is made with 6 inches of concrete, backed up by rebar, it provides a stout shell.
The PVC membrane both builders use comes in strips that are welded together onsite using a heat gun. With a little instruction from the manufacturer, builders get the hang of it.
"Our team received manufacturer training and even assisted our initial installations to ensure we were doing everything correctly which helped cultivate a sense of confidence in our procedure," explains Teinert. "There is a learning curve, like anything else. However, pool professionals need to understand it is not that difficult, and there is no need for expensive equipment."
"I found the heat gun to be intuitive, making the pool interior welding easy," adds Lavio. "But this winter, I will get more training to increase my speed and learn new techniques, tips, and tricks with corners, and other custom features on the pool to master the installation."
Lavio is able to install membranes in weather down to 41 degrees F, which is a crucial advantage in his northern climate. "Being able to install the PVC membrane in colder temps is very helpful for our company as we can build more pools later into the fall and winter, extending our construction season," says Lavio.
"We also do hotel and condo pools, as the reinforced PVC membrane is also commercially rated and great to use in renovations, especially on big, older concrete pools."