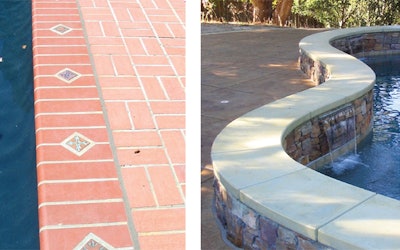
Sometimes the simplest construction details can be among the most important. Joints used to prevent and control damage in concrete structures are perfect examples.
We've seen them our entire lives in sidewalks, driveways, playgrounds, patios and swimming pool decks, and also in larger concrete structures such as freeways, bridges and parking structures. Joints in concrete are so common, few people pay much attention.
In the pool industry we deal with two specific types of joints: control joints and expansion joints, which are the most common joints used in all types of concrete slabs. Although the terms are sometimes (and incorrectly) used interchangeably, there are important differences between the two.
- Control joints traverse the slab, typically the deck, especially in pool projects. These joints are there to control the location and appearance of cracks, which are often due to concrete shrinkage and other factors related to expansion and contraction. They can also reduce the impact cracks have on the "performance" of the slab or other type of structure, even though they are primarily there for aesthetic reasons.
- Expansion joints accommodate normal movement of adjoining concrete structures. They are the critical buffer between pool decks on one side, and the tile line, coping and mortar bed on the other. In areas with expansive soil, including most of California where I work, expansion joints are particularly important, but the same can be said for areas with freeze/thaw conditions.
For as common and relatively simple as control and expansions joints are, it can be surprising how often I've seen mistakes that result in damage. Like so many points of craftsmanship, using joints correctly is a basic matter of education, dedication to quality and on-site awareness.
There's nothing complicated about them, but you do need to mind the basics during both installation and later on when making repairs.
This expansion joint gap is ready to be filled with foam and mastic.
COSMETIC TO CRITICAL
Starting with control joints, there's typically not that much refurbishing you can do once they're installed. When the slab cracks, and they always will at some point, the only way to mitigate the problem in a structural way is to remove and replace the entire section. As a result, a lot of people just live with the cracked concrete, especially in a slab where it's usually only a visual annoyance.
In an effort to make an existing deck look like new, there are companies that will apply topical overlays to bridge unsightly cracks. Although there have been improvements in the preparation and application techniques of various overlays, it's been my experience that in time, the crack will often reappear through the overlay.
RELATED: Perfecting Placement: Shotcrete Application Basics
Where control joints are concerned, there are two big mistakes I've seen:
- Joints that are installed too far apart, which allows a crack to appear between the joint.
- Joints that have been cut too shallow and thus don't adequately pre-weaken the slab at the location of the joint. As a result, cracks form elsewhere.
(The standard for joint spacing is 1.5 x the width of the slab. E.g. if you have a 4-foot skirt of decking, the joints should traverse the deck at no more than 6 feet apart. A similar ratio applies to larger slabs for joint spacing.)
Expansion joints are much different and, frankly, far more important, especially around pools. They are critical to the long-term performance of the coping and tile line. Most people are probably familiar with the type of joint at the back of the coping that encircles the pool, typically filled with some type of flexible buffer material and sealed with flexible mastic.
(Top) Here the expansion joint is doing its job of preventing the deck's movement from damaging the coping and tile. (Bottom) Damage caused by deck movement can be severe and is commonly revealed in cracking at the tile line.
(There are other types of joints but we'll stick with this most common type for the sake of this discussion,)
The whole point of the expansion joint is to separate the top of the shell, mortar bed and coping from the deck. Any time the deck impinges on the back of the coping and mortar bed, damage is almost certain to occur. I like to see a gap that's ½-inch wide between the deck and the coping. The gap should extend downward through the entire depth of the slab, usually about 4 inches.
The degree to which that does not exist directly correlates to how much damage there will be as a result of deck movement. There are some decking contractors who just don't get it and pour the slab right up against the coping. That usually results in severe damage. (It's fair to say that those contractors have no business working around pools.) The complete absence of an expansion joint around a pool or other hardscape structure abutted by a deck is a blatant workmanship fl aw and should never happen, although amazingly it sometimes does.
More common are situations where the deck installer tried to do the right thing by installing an expansion joint but made one of two common errors. First, they may have "underpoured" the joint, creating what I call a "tangent" of concrete that reaches beneath the joint material and touches the backside of the pool structure. It looks like an L-shape from the side view, extending laterally underneath the joint's gap. The tangent concrete then presses against the coping and/or the mortar bed, causing damage when the deck moves laterally, essentially rendering the joint useless.
From above, it looks like there's a joint there, but functionally there isn't. You can take a knife or skinny screwdriver and sink it down into the joint to tell if the gap extends all the way through the slab, or if there are places where the slab touches the back of the coping and possibly the mortar bed.
RELATED: Case Study: Repairing Structural Cracks
The other common mistake is the decking contractor again has the right idea but uses concrete nails to attach the fill material to the back of the coping. (I prefer PolyVoid by Stegmeier or Deck-o- Foam from W.R. Meadows to fill the joint. Regardless of the manufacturer, you always need a flexible foam-like material.) The nails completely defeat the point of the expansion joint by giving the deck a way transmit the energy of its movement to the pool. Either problem can quickly lead to a domino effect. Once the deck starts dislodging the coping and tile in one place, it can then move sequentially down the run of the pool from that initial point. All it takes is one nail or one spot with a tangent to start a run of coping stones becoming dislodged.
The concrete tangent – now visible (L) with the delaminated coping pieces removed - transfers energy from the deck movement to the pool, which results in damage to coping and tile (R). (The same thing happens when concrete nails are used to attach the foam filler material to the back of the coping.)
NATURAL MOVEMENTS
When you work in an area with expansive soils, it should be routine to prepare the site for those conditions. In addition to properly installed expansion joints, we make it a point to prep the deck area with 4 inches of compacted base rock and then saturate the soil for three days. We stop watering the area on the fourth day and pour the deck on the fifth – all to make sure the soil is pre-saturated and moisture conditioned as much as possible.
There are situations where the ground is going to move despite your best efforts to mitigate it with subsurface preparation. When that happens, the expansion joint becomes the only thing preventing significant damage, which will be all the more costly when the pool includes expensive tile work or coping material. For any pool, and high-end work especially, expansion joints are extremely affordable insurance.
In most cases, we find problems when homeowners contact us because their tile is coming off or cracking. On those calls I always suspect a problem with the expansion joint because tile does not typically fall off or crack all by its own volition. Once on site, I'll tap on the coping with a heavy broom handle (or softly with a hammer) because you can easily hear where the joint is hollow and delaminated or still well adhered. Almost invariably, where there's a hollow sound, you'll also fi nd a horizontal crack present in the tile line about a third of the way down from the top, or at the top of the tile line, if we're lucky.
If you look at it from the side, you can see that when the deck pushes on the mortar bed, it's going tousually delaminate it from the top of the bond beam, which creates the crack that becomes visible in the tile.
It's important to note that when cracks form, they provide a place where pool water can then intrude into the mortar bed and eventually saturate the surrounding soil, where it can exacerbate soil expansion.
GAP MEASURES
The extent of the damage is determined by how the movement of the deck is manifest in the pool. Sometimes there's only a small tangent, for example, and you only need to reset a couple coping stones and correct the joint in that spot. More often than not, however, we find the problem around most or all of the pool because the expansion-joint methodology and/or placement was wrong to begin with. If the contractor failed to do it right in one spot, odds are it's wrong elsewhere.
First, you do whatever is needed to lift the coping. That usually means saw-cutting the grout join on either side of the piece you want to remove. Because it's delaminated, it'll almost always just lift right off.
RELATED: The Trouble with Tile Installation
Then inspect the expansion joint area and determine what's causing the problem. The simplest fix is to remove all the nails — if that is indeed the cause of the problem. If the problem is an under-poured tangent, which can also include steel from the deck that's protruding through the joint, that means taking a concrete saw and cutting off what's there so the edge of the deck is flush, thus creating the necessary gap.
Basically, you just remove offending element. Once that's done, you know you have a proper gap that will protect the pool from further normal deck movement.
From there, reset the coping in whatever way is appropriate based on the damage and re-install the tile. (Tile and coping repair are separate subjects and beyond the scope of this article.) The closed-cell foam material, as mentioned above, typically comes with a tear-strip we orient toward the top of the joint. Once the deck is placed, this enables us to remove that tear strip, which provides a gap that we then seal with a mastic material. Over the years, I've typically used Deck-O-Seal or Sikaflex self-leveling mastic.
Sealing the joint with mastic is important because it prevents water from penetrating the joint. It's available in a variety of colors that can be matched to the particular environment. Additionally, as the mastic begins to set, you can top-sand it to give the joint a more natural, grout-like appearance while still maintaining flexibility.
When all is said and done, the surest way to approach the work is to protect structures in the landscape — not only pools but other hardscape features — from possible deck movement with the use of expansion joints. It's not hard, you just have to mind the gaps.