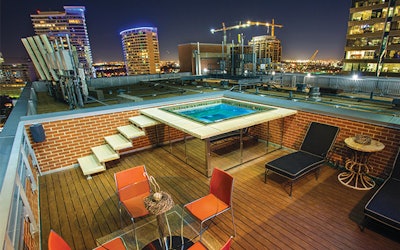
The project you see here looks clean and elegant, but make no mistake: It certainly wasn’t easy to achieve. A small 20-by-30 foot deck, unusual material selections, a concurrent interior remodel and a homeowner’s association were just a few challenges the Pool Environments team (Plano, Texas) faced.
Then add in the height factor. This project was 270 feet, or seven stories, off the ground.
“It was a challenge from the start,” laughs Reconstruction Project Manager Mike Murphy.
Luckily, the team’s efforts paid off as this installation took home a bronze award in this year’s Awards of Excellence. Here, Murphy walks us through the project’s design and installation from the initial demo work to the final touches.
Groundwork
Before this patio became the rooftop oasis that you see here, it was a plainer-looking space with a portable spa and wooden deck. The first step of the reconstruction process was gutting the tub: disconnecting the electric, removing the pumps and, finally, sawing it apart with a concrete saw, which allowed the team to take it down the service elevator in manageable pieces.
After removing the wood flooring, the team inspected rooftop liner, checking for faults in the waterproof seal.
“We opted to go ahead and just have it redone,” Murphy says. “So basically we put in a new roof liner, a new everything, to make sure that everything was tightly sealed, because this is sitting above someone else’s living room in the building.”
At the same time the patio was renovated, the interior of the home was also getting a facelift. A simultaneous indoor/outdoor renovation stretched the project timeline to six months, but did offer benefits. Working in tandem with the interior contractor, for example, ensured it was possible to bring enough power to the patio space to create a new service panel for the spa and outdoor lighting.
“What would’ve been simple was to buy a freestanding spa, go up there and sit it in place, plug it in and have a nice day,” Murphy says.
“There were lines that had to be brought out of the building and dropped down to the floor of the rooftop and then brought across, and everything had to be sealed and anchored. So it’s more of a commercial-type installation.”
RELATED: Hot Tub, Haute Look
A Big Haul
Once everything was cleared out and the new roof liner installed, it was time to schedule the lift. For Murphy, it was a juggling act of tasks: securing a crane, getting permits in place and ensuring police would be there to direct traffic around the lift site.
Nearly two semi-loads of materials needed to be lifted 270 feet in the air, swung over the site and placed down.
“It was done in stages,” Murphy says. “We lifted the spa first and then we lifted all the wood and framing materials for the underpinning of the deck second. And they were stored on plywood just outside the brick wall and then covered.”
The lift was completed over the course of seven hours.
“It actually worked out beautifully. I couldn’t have asked for it to go any more smoothly,” he says.
RELATED: Project Profile: A Steep Challenge
Design Elements
During the design phase, the homeowner made a request Murphy had never encountered before: mirrored siding for the hot tub.
“With these homeowners, you pretty much say, ‘Yes sir, that’s what we’re going to do.’ And then you figure it out and make it happen,” he says.
Actual mirrors were out of the question due to glare and fragility. After speaking to several glass companies and coming up empty handed, Murphy turned to a friend in commercial construction who suggested the winning solution: high-tensile-strength mirrored glass, the same you’d find on the exterior of a commercial high-rise.
The glass was cut and sanded on-site, and then mounted to the stainless-steel frame with metal strips and anchors, which were fabricated on site. Two of the glass panels can be removed by unscrewing the anchors for access to the spa equipment.
The enclosed skirt, however, required a bit of extra work.
“Obviously there was equipment running underneath there, so there’s an airflow problem,” Murphy says. “So we had to mount fans underneath it, which come out in various cracks that are hidden underneath the stone coping. Basically it’s a forced air system.”
For the patio flooring, Murphy turned to kwila wood, a heavy, high-density wood known for its weather- and insect-proof structure. (In fact, it’s heavy enough that the wood supply needed to be split up into two separate lifts to safely reach the roof.) While the decking appears to cover the entire 20-by-30 foot patio, it actually frames the spa, which rests on a high-load extruded foam for load-bearing purposes.
The stair design was developed largely on the fly. The original plan was to mount the steps to the brick wall with struts for added support. But when the homeowner’s association prohibited the team from attaching anything to the brick wall, the team adapted with a new design that utilized the spa’s stainless steel framework as support.
“We had this stainless steel framework made so the stone could sit on it and appear like it was just floating,” Murphy says.
While the stair design didn’t go exactly according to plan, the minimalist look combined with the mirrored siding lends a sense of openness to the patioscape, and helps it appear larger than it actually is.
“The homeowner absolutely loves it,” Murphy says. “He’s had nothing but good things to say about us.”
Comments or thoughts on this article? Please email [email protected]